Following the annual BTA Conference, Edwin Lampert from Riviera Maritime has composed an article on the presentation by SCHOTTEL’s Jörg Majewski and Julian Kimmerl regarding hybrid technologies for tugs.
The BTA extends its gratitude to the speakers and Edwin for their expertise and professionalism, which contributed to the success of the conference.
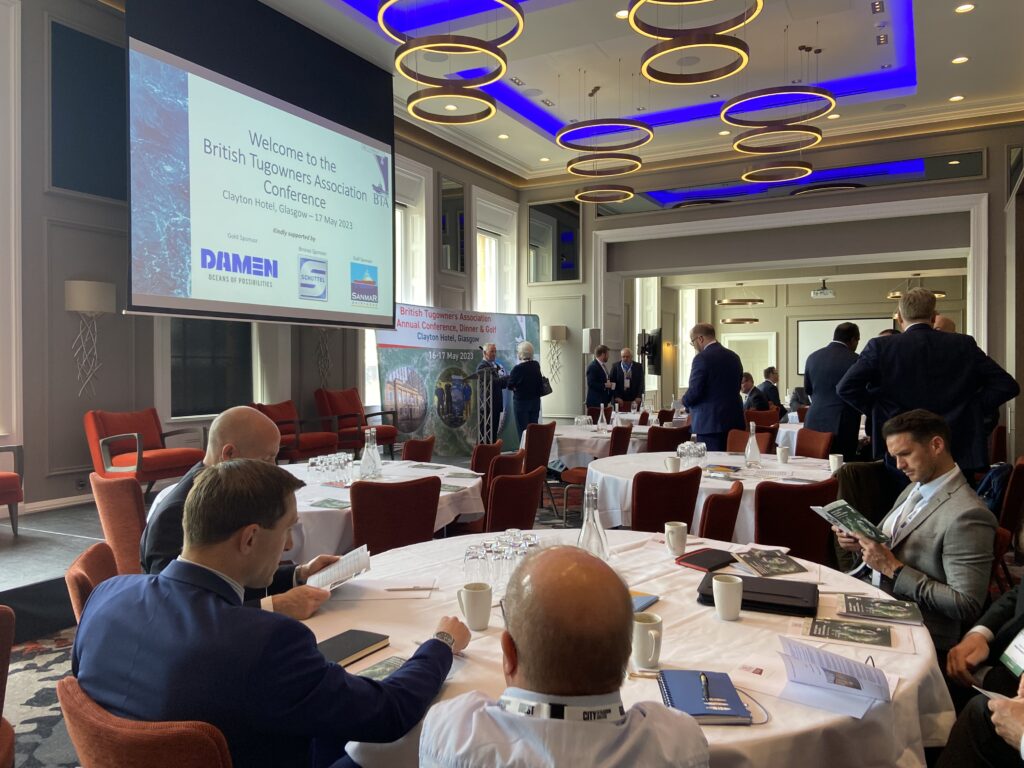
“Tugs are ideal candidates for hybrid drives,” stated Schottel sales director Jörg Majewski. “Why install maximum bollard pull power capacity when it’s only required perhaps 7% of operational time for ship-assist manoeuvres? Most of the time, a tug requires lower thrust, is in transit or loitering.”
Mr Majewski explained a key advantage with hybrid systems is they allow for a smaller main engine to be installed, supplemented by an electric motor or auxiliary engine to provide the peak power required when necessary. “We developed a mechanical hybrid, adding a gearbox link between propulsion units and auxiliary engines or generators. The built-in clutches smoothly engage supplemental power when increased thrust is required for harbour ship handling.”
Mr Majewski went on to tout mechanical hybrid’s advantages as substantial fuel savings, reduced maintenance costs through cutting engine hours, and lower emissions from operating smaller prime movers. “It’s a proven, safe and simple system,” he remarked, “offering redundancy for uninterrupted harbour operations.”
However, limitations exist too. As Mr Majewski acknowledged, “There’s no capability for zero-emissions operation with the mechanical-hybrid configuration.” All-electric hybrids address this shortcoming but raise other challenges.
Mr Majewski said the company’s electric-hybrid drives utilise compact, modular electric motors integrated into gearboxes. “Power sources can be batteries or generators installed to suit operational needs,” he added.
Modular, building-block designs also allow for a phased approach to sustainable operations. “Start with lower-emissions generators, then later add batteries for zero-emissions capability when technology matures,” said Mr Majewski. “It’s about configuring hybrids to match operating profiles and preparing assets for the future.”
Matching propulsion systems to duty cycles is crucial. “There’s no single solution,” advised Mr Majewski. “Requirements vary widely between a harbour tug and oceangoing salvage tug.”
Harbour tugs operate locally with frequent cycles manoeuvring ships in confined areas, meaning manoeuvrability and low-speed control are critical requirements. In contrast, salvage tugs transit longer distances and need sustained open water performance. Harbour tugs undergo high load variability during ship-handling operations, whereas salvage tugs require steady continuous power for long-distance towing. Oceangoing or salvage tugs also face rougher sea conditions, necessitating larger power reserves and redundancy, while harbour tugs typically stay closer to shore.
Additionally, harbour tugs will have readier access to shore power for recharging and maintenance where available, while salvage tugs operate remotely for extended periods. Finally, due to distinct operating profiles, different tug types have different stability needs.
“As regulations tighten,” said Mr Majewski, “hybrids provide a flexible bridge to cleaner tugs while protecting owners’ investments long term.”
Beyond emissions, underwater radiated noise (URN) has become a regulatory priority, evidenced by the recent agreement of new voluntary URN guidelines at IMO. Modelling and simulation tools are being used to design tug propellers with minimal noise-generating cavitation.
“With CFD, we can optimise for efficiency while reducing acoustic emissions,” explained Schottel research and development engineer, and specialist in hydrodynamics and propeller design, Julian Kimmerl. “This lets us engineer purpose-built tugs, balancing performance with environmental impacts.”
Schottel’s hydrodynamic simulations visualise propeller noise contributions and interactions. “We’re researching live onboard monitoring to continually tune operational noise,” Mr Kimmerl added.
Active noise control may provide another solution. Mr Kimmerl described active systems using opposing sound waves to destructively interfere with, and cancel out, cavitation noise.
“Prototype testing proved active control’s potential to eliminate up to 70% of cavitation noise,” said Mr Kimmerl, adding the company is now looking to commercialise the technology.
Looking ahead, stricter noise limits in sensitive regions will be introduced. By deploying CFD simulations during the design process, propellers can be proactively engineered to produce less underwater noise pollution and meet expected acoustic regulations even before they take effect, and avoid the requirement to retroactively modify propellers later to comply with new rules, added Mr Majewski.
Tighter emissions and ecological regulations will profoundly impact tug design, building and operation going forward, he added. Hybrid propulsion, simulation tools and active noise cancellation can help the global tug industry chart a more sustainable course while extending asset lifecycles, agreed Mr Kimmerl. But technology is only part of the solution. “To decarbonise efficiently, we must collaborate across the value chain,” he added. “All stakeholders, from regulators to designers to owners, need an integrated approach.”
The articled can be found on Riviera’s website here – Riviera – News Content Hub – The case for hybrid technologies for tugs (rivieramm.com)
With gratitude to Edwin Lampert and Riviera for granting permission to the BTA to publish the article.